At LPN Plate Mill, in process of hot rolled steel plate, we attend to develop our steel industry goes hand in hand with development our social, communities and natural environment. Pollution is prevented and controlled in order to has minimum detrimental effect for social, communities and surrounding environment including to promote the awareness in efficient use of resources and energy through employees and publication.
Ever since the construction of our plant, LPN has been in strict compliance with all laws and environmental regulations. We have constantly made an environmental assessment impact report (EIA) and carried out inspection and measurement for air and water quality as specified in EIA report. The measurement result is reported to the Office of Natural Resources and Environmental Policy and planning every 6 month and plan to take corrective and preventive action when necessary. Moreover, the company has to encourage waste management program and promote 3R knowledge to our employees.
We implemented the environmental management system to be the foundation for minimizing the environmental impact from our processes including third parties activities who work on behalf of the company. Our achievement has started since 2004 when we were granted the ISO 14001 certification.
Environmental impact controlling and minimizing countermeasure
The company appointed an independent expert in environment to inspect its environment quality . The monitoring and supervision are planned for;
- Monitoring of an air emission quality (from stack)
- Monitoring of an air ambient quality
- Monitoring of an air quality in workplace
- Monitoring of noise level
- Monitoring of concentrated light
- Monitoring of workplace temperature
- Monitoring of water quality (before and after treatment)
Waste management program
Most of non-hazardous wastes from manufacturing process such as scale, scrap, iron oxide etc; can be recycled and will sent to reforming or recycling process in others steel industries. Hazardous wastes such as roll grinding sludge, used oil and grease, waste water treatment sludge including chemical contaminated wastes are sent into industry type 101 and 105 that was already registered by the Department of Industrial Works.
Water quality control
Contaminated water in manufacturing process is drained into an Oil Separator Sump where iron scales are sediment and oil is separated from water surface. After this, the water is released into an Oxidation pond for chemical treatment before circulated to process without discharging to pubic waterway.
Other consume water is treated in waste water treatment system with biological process. After this, the water is used for dust removal and watered most of plants within green areas.
Air quality control
Air quality from manufacturing process has countermeasure to control and measure of combustion system. Bunker oil which is selected to use as fuel shall composed of sulphur not exceed 2% and steel reheating temperature is controlled between 1260 + 10 °C. An exhausted air from reheating furnace stack is monitored and measured every 6 month.
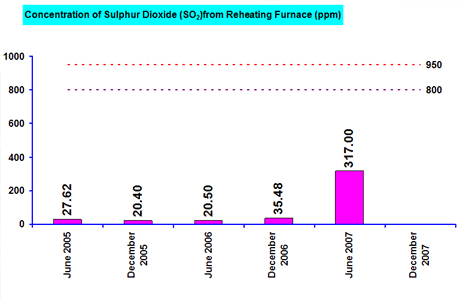
- Standard from Ministry of Industry
** Standard from Ministry of Sciences and Technology
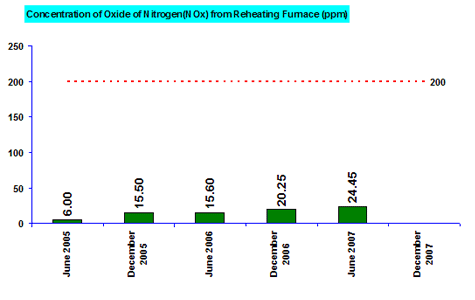
Remarks : Standard from Ministry of Industry and Ministry of Sciences and Technology
Resource Consumption and Energy Conservation
Since 2005, LPN Plate Mill Pcl., has established the department of energy conservation to respond the country intention in resource and energy conservation. The department has responsibilities to undertake the policy from top management and government regulations to implement through the company including to consult the energy conservation technique and energy compensation, encourage the conservation awareness though an organization. The energy conservation committee , consisting of representative from related departments, has appointed to control and assess the efficiency from conservation program and including to continually develop in energy conservation.
The way for energy and resources conservation to be continue
- Saving of water
- Saving of electricity
- Saving of paper
- Minimizing of fuel oil(bunker) , diesel , lubricant , grease and LPG gas
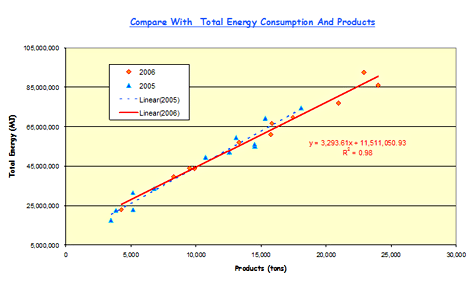